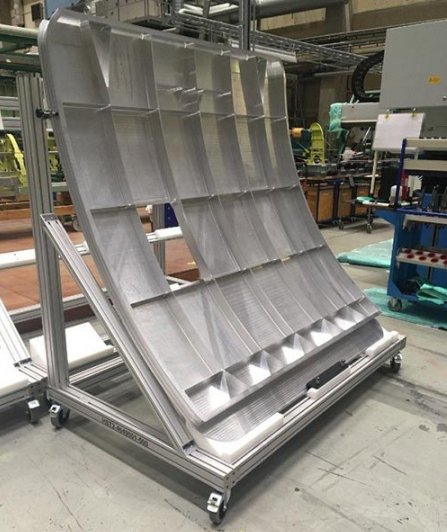
Lightweight materials and efficient manufacturing bring environmental benefits to cargo doors
A major delivery was made recently in Clean Sky 2’s work on the next generation of cargo doors and aircraft structures, which is being led by Saab together with several partners. In January 2020 the latest demonstrator component, the TD 3 structure (a high-energy hydroformed and machined door), was delivered to Saab from the company 3D Metal Forming, part of the MISSP project led by Sonaca.
The doors being explored provide a platform for new innovative design solutions but also serve as a demonstrator for new technologies, materials and manufacturing techniques applicable for generic airframe structures. A reduced environmental footprint for the aircraft industry is one of the key drivers for the technologies included in the project.
Five door demonstrators will be manufactured. Three will be purely structural, showcasing new/upcoming metallic manufacture technologies and materials. Two will show a novel cargo door configuration with full functionality (opening, latching & locking systems); one of these will be a metallic solution and the other composite. Collaboration between Saab Aerostructures and Airbus will result in the demonstration of these functional cargo doors in representative metallic and composite fuselage sections.
The structure recently delivered to Saab has an integrated skin, frames and stringers, greatly reducing the part count for a typical skeleton structure. Although hydroforming is not a new forming process, developments in automated high-speed machining over the last decade have made this type of integrated structure much more advantageous from a design, assembly, and cost perspective. The large reduction in the number of fasteners and sealant provides an efficient, lightweight structure with less complex stress calculations. The structure also has major advantages in terms of assembly and the tolerance variations typically seen when multiple parts are assembled together